Block Printing: Old, Simple, Stunning
How much do you know about the age old, traditional and labor-intensive process? We thought a quick education as to how it all goes down would be noteworthy.
We sat down with textile designer Brook Perdigon owner of Brook Perdigon Textiles who walked us through the block printing process to shed some light. Brook spent time in India in 2016 completing an education in traditional Indian methods of block printing. What she learned in her travels was fascinating and a bit surprising.
The general process of block printing breaks down like this:
- A hand carved wood block is dipped into a dye pool, stamped on a fabric and repeated until that color is complete for the pattern.
- The cloth is then dried and the stamping process is repeated for each color, dried in between, and the full process is repeated for any additional patterns + colors that are a part of that fabric’s overall design.
- The fabric is then dipped in a solution bath to set the ink, then hung to dry.
The Process
It's not quite that simple...
While the process seems relatively straight-forward (however laborious and time intensive), what’s surprising is the amount of accuracy that is required by the printer to get a somewhat even consistency of pattern and ink application/distribution.
A printer will dip the block into a small vessel of dye, being careful to pick up the exact amount of dye needed, then take the block directly to the cloth and stamp exactly where the next pattern appears in the design. There is no system for controlling how much dye is applied to each stamp before hitting the cloth. The printer relies on their feel and experience for accuracy and control of how much dye they pick up on the block.
This is hard!
When Brook tried her hand at printing with blocks she was amazed at how challenging it was to accomplish this, “They made it look so easy that I couldn’t believe how challenging it was to get any sort of consistency when I tried the process myself. It was bananas!”
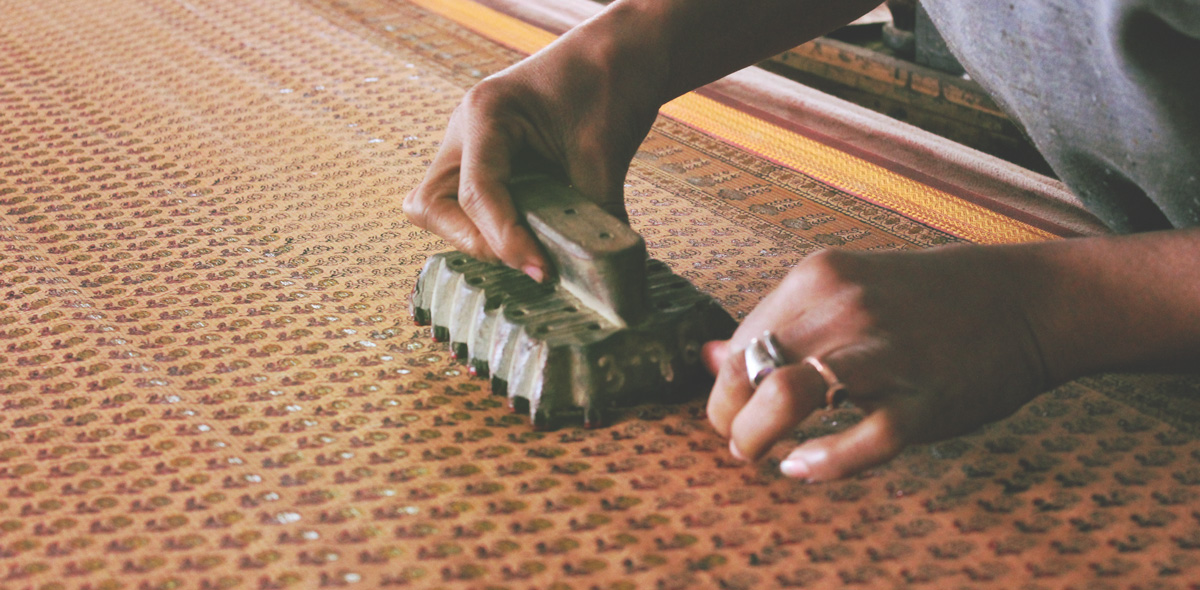
No guides. No nothing!
Likewise, a printer typically doesn’t rely on any sort of system to guide them as to where to stamp the fabric with the block to align the pattern. They simply rely on the accuracy of their eye and sense of feel for the block being used.
So imagine that a yard of hand block printed fabric may contain multiple stamps of numerous patterns to create the overall repeat. For each of the stamps, the amount of dye and the location of each application is completely eyeballed.
Um...she got the hang of it.
Got Blocking Skills?
Having said all that...what is so attractive about block printed fabric is the inconsistencies, the variation of color saturation and the one-of-a kind results. Its no surprise that this method of printing continues to be so relevant and revered. Tell us, how do you use block printed fabric in your projects?